Bashō-fu

A type of textile typical to Okinawa. Tough, stiff, and light: in the bygone days, it was used in all sorts of sectors from workwear to clothes for the upper classes and was produced throughout Okinawa.
In order to weave them, plantain fibers are stripped with nails and made into a yarn of even thickness. Plantains are vulnerable to aridity and easy to snap, so they must be moistened with a spray while weaving. Bashō-fu is a textile that requires perseverance, effort, and affection.
Its production is extremely limited today: Kijoka in Ogimi village, Yanbaru, is the most lively production site, and in fact the only production site actually. Its difficulty in obtaining the materials—requiring 200 plantains for a roll of kimono textile—may be one of the reasons why, but also the great work it takes for its completion may be another.
All of its procedures must be done by hand. Hence, it is not suited for mass production, and all of the social/economical structures of the present day are oppressing the production of bashō-fu. According to Taira Toshiko, who seems to have dedicated her life to this textile, plantain fields are gradually diverted to other purposes, and wood ash used to boil woven textiles are getting harder and harder to find.
Today’s yearly production is 350 rolls (article written in 1992). This figure is realized thanks to the determination of Taira and the people of Kijoka—while spinners are aging every year, there is a limit to weavers that can be trained.
Consequently, the extreme scarcity of the textile is leading to a rise in price. However, it is also a fact that without some supply, no greater demands can happen.
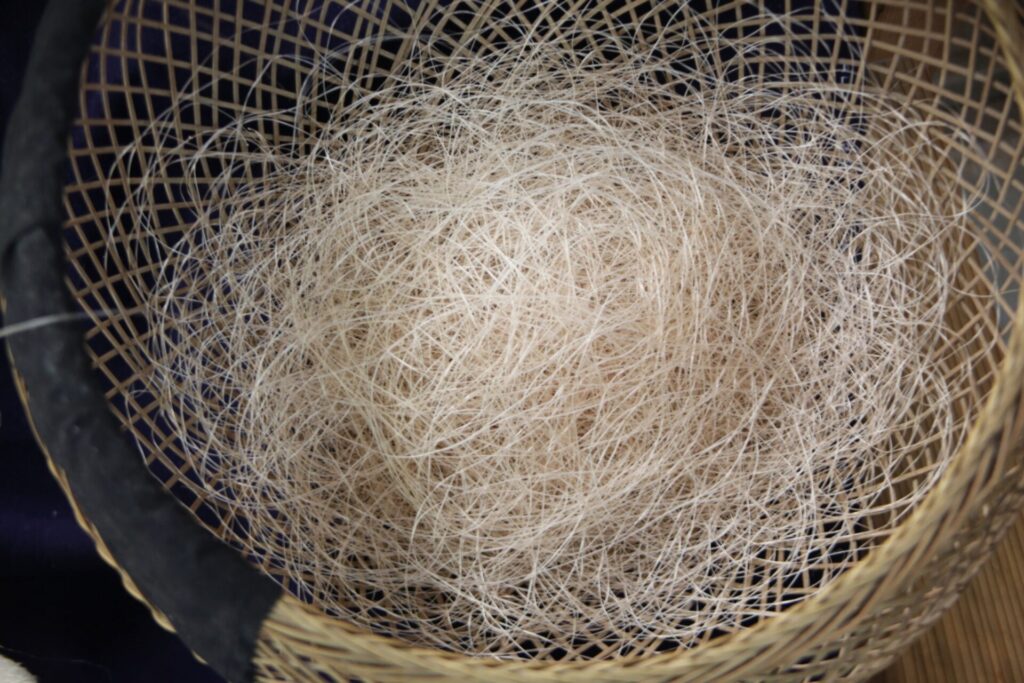
Behind this unique village where the bashō-fu production remains, and the people who have maintained it, are the encouragement and support from the former head of KURABO INDUSTRIES of Kurashiki, Ohara Soichiro, and other people from mainland Japan. For Taira and others who had gone to Kurashiki during wartime as a member of the women’s volunteer corps, Ohara and his team promptly supported them to construct a studio for tests after the defeat in the war and prayed for the rebuilding of Okinawan culture as the girls headed their homeland: all of this to not to put an end to the Okinawan tradition of bashō-fu.
Taira has responded to this support by being the leading figure in the rebuilding and development of bashō-fu, and in 1974, was designated the Important Intangible Cultural Properties of Japan as the Kijoka Bashō-fu Preservation Society. Taira did not mention any individual credits but always put the pride and honor of her village first, and the appreciation and support given to her way of living led to the survival of the only production site. In a way, via the Pacific War, bashō-fu is the one and only virtue the mainland has offered to Okinawa, kept and grown by the hands of Kijoka people.
There are no usual designs on bashō-fu like there is on kasuri1. The drawings are intentionally woven in by moving ikat woof as desired. Therefore, its patterns are dynamic and fully impromptu.
This textile is easily creased, and it is said that when you sit down, you must stand up while stepping on the bottom—however, this is only true for ryūsō, the Ryukyuan style. In matters of kimono, you cannot step the bottom of the fabric because it’s tucked up.
Other than kimono, obi (kimono belt) or centerpieces are produced on the side and loved as a textile reflecting the abundant nature of Okinawa.
Editor’s Note:
- Kimono cloth with splashed patterns.